Armado con una impresora 3D modificada, el constructor de PC Jean Roberto De Lacovo creó todas las piezas que necesitaba para fabricar el chasis de este impresionante Caja de PC impresa en 3D. Se llama Piñasphere y cuenta con una APU AMD Ryzen 7 de 8 núcleos refrigerada por líquido.
Gracias a nuestra página de Facebook de construcción de PC de rápido crecimiento, hemos visto muchas PC para juegos personalizadas, desde modificaciones basadas en diseños de carcasas existentes hasta versiones preliminares. Incluso puedes enviar el tuyo para su consideración aquí mismo. Por ahora, descubramos cómo Jean hizo esta impresionante carcasa para PC impresa en 3D.
PCGamesN: ¿Qué te inspiró a construir esta PC?
Vaquero: Quería ver hasta dónde podía llegar con el diseño de una carcasa de ordenador. El estándar que la gente imagina cuando habla de un PC es una forma de caja; salvo muy pocas excepciones, la mayoría de las carcasas de ordenador tienen una forma cuadrada.
A los lados puedes ver estos anillos negros ondulados; quería que se parecieran a las ondas que se generan cuando dejas caer algo al agua. Ya estaba jugando con el motivo de piña para la cúpula en ese momento, así que pensé que esta idea funcionaría muy bien también para las crestas de las olas, aunque con muchos ajustes.
La otra mitad de la cúpula también estaba inspirada en la naturaleza: está basada en panales rellenos y cada hexágono es complejo cuando se ve de cerca. Esta complejidad también ayuda a la hora de hacer que las líneas de la capa de impresión sean menos visibles. El interior tiene un aspecto más de ciencia ficción con muchos polígonos. Es estructuralmente similar a la estructura de un avión: no es una esfera, sino una icosfera compleja con agujeros geométricos que también ayudan con el flujo de aire.
¿Cómo planeaste y diseñaste esta construcción?
Normalmente comienzo mi trabajo con algunos bocetos rápidos en lápiz y papel, pero este comenzó con un boceto en Tinkercad. Estaba probando varias configuraciones con algunas maquetas 3D que hice de los componentes de hardware en Tinkercad, luego pensé que si no instalaba una GPU y usaba una fuente de alimentación externa, podría intentar crear una forma de esfera dividida.
La primera idea fue utilizar una estructura metálica artesanal realizada con chapa de aluminio de 3 mm de espesor. Sin embargo, recientemente también hice algunos experimentos con impresión 3D para hacer un equipo de cámara; durante esos experimentos probé la resistencia del PLA y el PETG, y concluí que el PETG era lo suficientemente fuerte como para soportar las tensiones de la carcasa.
Utilizaste impresión 3D para toda la construcción; cuéntanos todo sobre tu proceso.
Al principio fue difícil, pero ahora sería un proceso mucho más rápido, tuve que empezar a planificarlo de manera diferente a un mod de caso habitual, porque no estaba quitando material sino añadiendo. Hice algunas pruebas con diferentes proyectos pequeños para poder ajustar la configuración de la impresora 3D.
El software que utilicé como cortador para las impresiones fue Ultimaker Cura 4.13, lo encontré intuitivo desde el principio y me permitió afinar mis impresiones. Por ejemplo, aprendí a configurar la alineación de la costura en Z para evitar tener una línea visible en las impresiones y a configurar los ajustes de retracción para diferentes situaciones; básicamente, puedes adaptar los ajustes a tus necesidades.
Mi impresora 3D más potente es una Creality Ender 3 Pro, que modifiqué porque era demasiado ruidosa para mí. Agregué una placa base Creality Silent, además de un ventilador de 120 mm para la fuente de alimentación, y también diseñé e imprimí los conductos de ventilador personalizados para la impresora con PETG, lo que me permite usar una configuración de ventilador dual Noctua de 60 mm en lugar de los ventiladores estándar de 40 mm. .
Ahora también tiene un extrusor directo: tuve que reducir la retracción mucho más de lo esperado, porque las primeras impresiones con la nueva configuración provocaron problemas de obstrucción del extrusor al imprimir con PETG.
En total, Piñasphere se compone de 27 piezas impresas en 3D. Para los toques finales utilicé cortadores de precisión, junto con un encendedor, para eliminar cualquier exceso de material o hilo. Sin embargo, una vez que obtuve las temperaturas correctas del filamento, descubrí que el encordado era extremadamente limitado.
También descubrí que la orientación de las piezas durante el proceso de impresión ayudó a la hora del acabado. Elijo a propósito la base como lado de contacto entre piezas, ya que es el lado con el que menos control tienes para el acabado si no lo pintas después.
Un punto clave que aprendí es que limpiar perfectamente las piezas con cortadores de precisión requiere tiempo y paciencia; comete un error y terminarás tirando la pieza impresa; sucedió con un marco SSD que imprimí. La limpieza y nivelación de la impresora también lleva un poco de tiempo, pero resuelve la mayoría de los problemas que pueden ocurrir durante el proceso de impresión; imprimir a una velocidad más lenta también ayuda a evitar muchos problemas.
¿Cómo encajan todas las piezas?
Básicamente se trata de una estructura tipo sándwich: al igual que en los aviones, algunas piezas simplemente se presionan entre las capas unidas. Las piezas tienen una forma que permite ensamblarlas únicamente de la manera correcta; incluso si se trata de una esquina o un agujero diferente, cada pieza siempre tiene un aspecto que ayuda a su posicionamiento. Esta estructura me permitió crear un chasis con suficiente resistencia, pero con un relleno mínimo, por lo que minimiza el peso y la cantidad de material utilizado.
Luego utilicé tornillos de acero inoxidable para la fijación (la placa base se fija con tornillos M3 con inserciones de latón roscadas de 10 mm); puedes calentarlos con un soldador y luego presionarlos dentro de las piezas impresas en 3D. Para el resto de las fijaciones, enrosqué el PETG con herramientas y utilicé tornillos de cabeza de botón M5; las secciones roscadas tienen al menos 10 mm de largo.
Mientras tanto, los domos blancos simplemente encajan en su lugar en el lado de la placa base y se aseguran con un ligero giro en el sentido de las agujas del reloj en el lado del radiador; aquí no se necesitan herramientas.
¿Qué pequeña placa base es esa?
Utilicé una placa base ASRock X300M-STX. Fue una de las placas base más pequeñas que pude encontrar y que me permitió usar un AMD Ryzen 7 5700G. Puede admitir hasta 64 GB de memoria y tiene dos ranuras para SSD M.2 y dos puertos SATA para SSD de 2,5 pulgadas, por lo que me brinda un amplio espacio para actualizar la memoria y el almacenamiento, lo que ayudará a que esta máquina siga siendo útil en el futuro. tal vez como PC de oficina o servidor.
¿Qué desafíos presentó la forma de la construcción?
Honestamente, si piensas principalmente en la forma y no en las dimensiones, es relativamente fácil hacer una PC con una forma inusual; el mayor desafío para mí fue dejar suficiente espacio dentro de la carcasa para que todo el equipo funcionara bien.
Otro gran desafío lo presentaron los dos paneles de E/S: había decidido que ambos se parecerían al panel frontal, colocados en un hueco del domo, pero también tenía que dejar algo de espacio para el cable de alimentación. , y es por eso que el ‘rebanado’ es tan largo de ese lado.
¿Qué fuente de alimentación usaste?
Es la fuente de alimentación externa que se envía con el ASRock Deskmini X300. Parece una fuente de alimentación para computadora portátil y su salida es de 120 W a 19 V; es bastante pequeña, por lo que era perfecta para esta PC, ya que no es un monstruo que consume mucha energía.
¿Cómo planificó el tendido de cables?
Todos los cables se enrutan dentro del anillo central, que también forma el marco principal; tiene muchos espacios vacíos para el flujo de aire y el enrutamiento de cables. Los cables para el interruptor de encendido, el LED de actividad del SSD y el LED de encendido están escondidos debajo de la placa base y luego van a la caja que actúa como ganchos para los domos y también contiene el interruptor de encendido.
El cable del ventilador del radiador está oculto por el gancho de la cúpula debajo del radiador (le hice un canal de enrutamiento), luego pasa por el pasaje de uno de los tubos de enfriamiento y permanece oculto debajo del tubo de enfriamiento en el lado de la placa base. Los cables de la antena Wi-Fi están ocultos debajo de la placa base y sus conectores en la parte superior de la placa base están ocultos debajo del SSD M.2 para que no puedas verlos. Por último, los cables del bloque de agua se colocaron debajo de las «alas» de sujeción del bloque de agua.
Cuéntanos cómo funciona el sistema de flujo de aire.
Esta es una de las partes que más me gusta de mis proyectos. Después de pasar por el radiador, el aire pasa por el canal central, enfriando el SSD de 2,5 pulgadas, luego pasa por debajo de la placa base y sale por un espacio de 5 mm entre la placa base y su marco de soporte: fluye alrededor de casi todo el perímetro.
Pero el aire no sale en este punto: el domo interno lo guía para que se mueva alrededor de la placa base, de modo que enfríe los módulos M.2 y el disipador térmico VRM de la placa base. También hay dos orificios en el costado del radiador, que alivian un poco la contrapresión generada por el aire que se mueve dentro del canal central.
¿Cómo lograste los toques color cobre?
Quería agregar un color cálido para contrastar con el blanco y originalmente consideré usar anillos de cobre reales. Sin embargo, durante la fase de boceto quise agregar más facetas reflectantes que las que se encuentran en los anillos, así que los imprimí con una forma más compleja.
Si hubiera tenido mucho tiempo, podría haberlos hecho a mano, pero esta vez quería ponerme a prueba y ver qué podía hacer solo con la impresión 3D, así que compré un filamento de cobre de seda Giantarm y los resultados no me decepcionaron. Le dan un ambiente premium a la construcción.
¿Qué especificación elegiste y por qué?
Quería que pudiera hacer un poco de todo, pero la edición 3D era una capacidad imprescindible. También quería que la máquina funcionara decentemente en juegos de 1080p. Sin espacio para una tarjeta gráfica, la elección obvia era elegir la mejor APU que podía comprar, y esa era la AMD Ryzen 7 5700G. Me encanta; es un excelente intérprete.
La versión tiene 16 GB de memoria porque estuve buscando el hardware durante octubre y noviembre y estaba a la venta en ese momento. Corsair es una buena marca, así que aproveché la oportunidad y la compré.
Actualizaré la RAM en los próximos meses, ya que la placa base ASRock te permite aumentar la RAM de video compartida hasta 16 GB si tienes más de 32 GB de memoria del sistema.
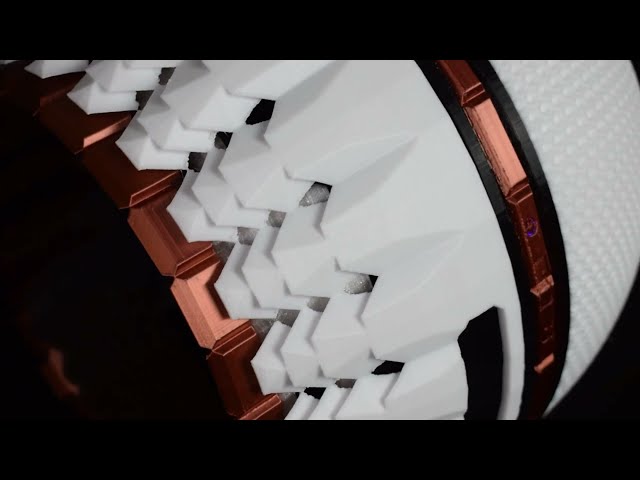
¿Encontraste alguna dificultad?
Creo que el mayor desafío fue ajustar el perfil de la impresora para cada filamento. Tuve que reducir los errores de impresión que serían imposibles de ocultar, ya que uno de mis objetivos era que la construcción se viera bien sin tener que pintarla.
Me acostumbré a limpiar profundamente la extrusora y también compré una aguja larga de acero inoxidable para eliminar todos los residuos de filamento.
¿Cuánto tiempo te llevó completar esta construcción, de principio a fin?
Después de la fase de aprendizaje sobre edición 3D, diría que 3-4 meses. Definitivamente tomaría menos tiempo si lo hiciera ahora.
¿Estás completamente satisfecho con el resultado final o desearías haberlo hecho de manera diferente en retrospectiva?
Estoy absolutamente feliz: era la primera vez que intentaba construir una carcasa impresa en 3D y antes del montaje final no estaba 100% seguro de cómo se vería. Sin embargo, después de ensamblarlo todo solo tuve un pensamiento: ‘¡Guau, es sólido y luce realmente genial!’ Realmente no podría estar más feliz.
Especificaciones de la PC impresa en 3D Pinasphere
- UPC: AMD Ryzen 7 5700G
- GPU: AMD Radeon RX Vega11 integrada
- Almacenamiento: SSD Samsung 980 M.2 de 1 TB, SSD SATA Samsung 860 Evo de 2,5 pulgadas de 250 GB
- Memoria: SODIMM DDR4 Corsair Vengeance de 16 GB (2 x 8 GB) a 3200 MHz
- Tarjeta madre: ASRock X300 M-STX
- Fuente de alimentación: Fuente de alimentación externa ASRock de 120 W
- Enfriamiento: Cooler Master MasterLiquid ML120L V2 Enfriador líquido AIO
Impresionante trabajo, Jean. Esta es una PC personalizada verdaderamente única: el diseño es excepcional y también has demostrado que realmente puedes hacer una carcasa de PC impresa en 3D increíblemente atractiva. también.
Esta publicación apareció originalmente en Custom PC, que ha estado cubriendo configuraciones increíbles durante más de 20 años y ahora es parte de PCGamesN. Únete a nuestro Grupo de Facebook de 500.000 miembros. para discutir esta construcción.
ISi se considera un experto en creación de PC, puede enviarnos su propia versión de PC personalizada hoy para tener la oportunidad de aparecer en PCGamesN en el futuro.